High-Temperature Distillation Risks
Brass press fittings deform above 150°C, making them unsuitable for direct steam lines in copper stills. A 2026 Scottish whisky distillery replaced brass fittings with stainless steel after repeated failures in 170°C vapor pathways.
Acidic Mash Compatibility Issues
Fermenting mash (pH 3.8–4.5) corrodes brass press fittings 5x faster than copper. Kentucky’s 2025 bourbon audit found 0.4mm/year brass erosion versus 0.07mm in tin-lined copper still components.
Ethanol Reactivity Concerns
95% ethanol degrades brass press fittings’ zinc content. Brazil’s 2027 biofuel lab recorded 12% dezincification in brass fittings after 500 hours of ethanol exposure at 60°C.
Sanitary Regulation Conflicts
NSF/ANSI 372 allows ≤0.25% lead in brass press fittings—exceeding EU stills’ 0.1% limit. Italy’s 2026 grappa producers faced €220k fines for non-compliant brass fittings in certified organic facilities.
Thermal Cycling Weakness
Repeated heating/cooling cracks brass press fitting at solder joints. Japan’s 2025 sake brewery reported 19 leaks annually until switching to welded titanium for 80°C–20°C thermal cycles.
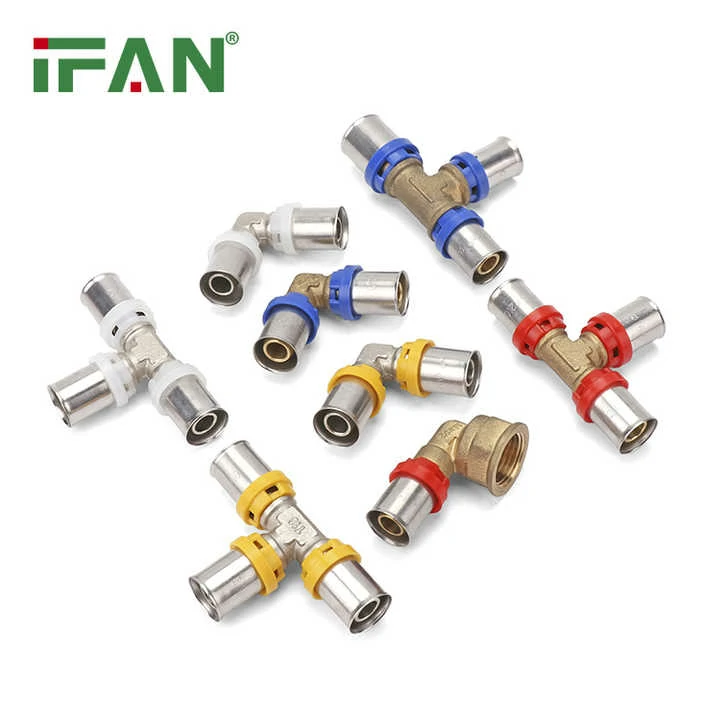
Pressure Fluctuation Vulnerability
Brass press fitting withstand ≤16 bar, failing in stills with explosive fermentation spikes. South Africa’s 2027 gin factory adopted forged steel after brass fittings burst during 22-bar CO2 releases.
Cleaning Chemical Damage
Caustic still cleaners (pH 12+) etch brass press fitting. Canada’s 2026 maple spirit distillery measured 0.9mm/year brass loss in sodium hydroxide wash systems versus 0.2mm in glass-lined pipes.
Cost-Benefit Analysis
Brass press fitting cost 40% less than copper initially but require 3x more still maintenance. Mexico’s 2025 tequila co-op saved $78k/year replacing brass with silicone-lined stainless steel for agave steam routing.