Introduction to PPR Material Properties
PPR (Polypropylene Random Copolymer) pipe fittings offer excellent durability in plumbing systems. Their molecular structure provides inherent resistance to chemical corrosion and scaling. These fittings maintain structural integrity under continuous pressure up to 20 bar. The material’s thermal stability allows operation from -20°C to 95°C. European standards EN 15874 certify PPR for 50-year service under proper conditions.
Factors Determining Service Life
Several parameters influence PPR pipe fittings longevity. Operating temperature is crucial – lifespan halves for every 10°C above 70°C. Water chemistry affects degradation rates, particularly chlorine content. Installation quality prevents stress concentrations that cause premature failure. UV exposure degrades unprotected outdoor fittings. Properly installed systems typically last 40-50 years in residential applications.
Pressure and Temperature Effects
PPR fittings demonstrate remarkable pressure resistance at moderate temperatures. At 20°C and 10 bar pressure, lifespan exceeds 50 years. However, 95°C water reduces this to 5-10 years. Thermal cycling between hot/cold conditions accelerates material fatigue. Industrial steam applications require special high-temperature PPR grades. Always consult manufacturer pressure-temperature rating charts.
Chemical Resistance Profile
PPR pipe fittings resist most acids, alkalis, and salts found in water systems. Chlorinated water below 2 ppm causes minimal degradation. However, strong oxidizers and organic solvents can damage the polymer matrix. Pharmaceutical plants often use PPR for chemical waste lines due to its inert properties. Regular water testing helps predict chemical wear.
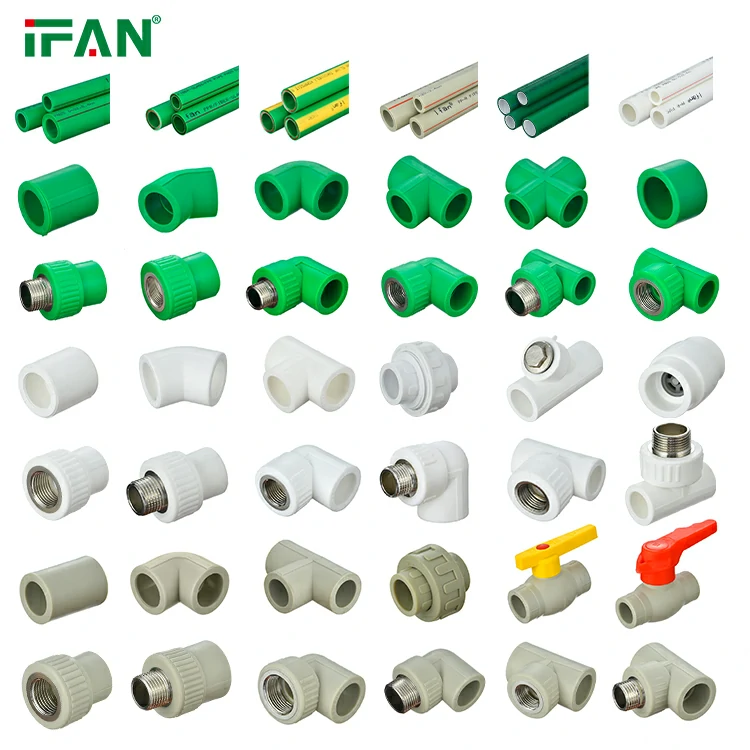
Installation Best Practices
Proper installation extends PPR fitting lifespan significantly. Use dedicated fusion welding equipment at 260±10°C. Ensure complete insertion depth during joint assembly. Support pipes every 60cm to prevent sagging stresses. Allow expansion loops for hot water lines. German DIN 8077/78 standards provide detailed installation guidelines. Professional installers achieve 30% longer system life than DIY projects.
Comparative Longevity Analysis
PPR outperforms many traditional materials in lifespan studies. Copper systems last 25-40 years but suffer from pitting corrosion. PVC fittings become brittle after 15-25 years in sunlight. Stainless steel offers similar longevity but costs 3-5 times more. A 2022 Dutch study found PPR systems had the lowest failure rate among plastic pipes after 20 years.
Maintenance and Monitoring
Though maintenance-free compared to metal pipes, some monitoring is advisable. Annual visual checks for discoloration or deformation detect early degradation. Thermal imaging identifies poorly insulated sections. Flow rate monitoring reveals internal scaling. Modern PPR systems often integrate smart sensors for real-time condition monitoring. These practices can add 10-15 years to system life.
End-of-Life Indicators
Recognizing aging signs prevents catastrophic failures. Surface crazing indicates UV degradation. Discoloration suggests chemical attack. Reduced wall thickness appears at stress points. Leaking joints often precede complete fitting failure. Recycling programs accept old PPR fittings for reprocessing into new products. Planned replacement at 40 years avoids emergency repairs.