Introduction to Plumbing Choices
Modern plumbing offers several fitting options for different needs.
Two of the most common are copper and PPR Fitting.
Copper has been used for decades in plumbing installations.
PPR Fitting is a newer material, gaining popularity worldwide.
This article compares both types to help users make informed decisions.
We explore material properties, installation, durability, cost, and applications.
Each system has strengths and limitations depending on project requirements.
Choosing between them depends on environment, budget, and usage priorities.
Material Characteristics
PPR Fitting is made from polypropylene random copolymer.
It is lightweight, corrosion-resistant, and thermally stable.
Copper is a natural metal with excellent heat conductivity.
It resists bacteria and can withstand high internal pressures.
However, copper may corrode in acidic or aggressive water.
PPR Fitting does not corrode or leach into the water.
It is also quieter in water flow compared to copper.
Both materials perform well but have distinct physical traits.
Installation Process
PPR Fitting is joined using heat fusion welding.
This creates seamless, leak-free, and permanent joints.
The process is fast, requires no threading or soldering.
Copper fittings need soldering with a torch and flux.
This requires more tools, skills, and safety precautions.
PPR Fitting installation is often quicker and safer on-site.
It also reduces fire hazards due to no open flame.
For large projects, this saves time and labor costs.
Durability and Service Life
Copper fittings are known for long-term durability.
They can last over 50 years in good conditions.
However, in acidic water they may erode or pit.
PPR Fitting is resistant to corrosion and chemical exposure.
Its smooth inner surface resists scaling and mineral buildup.
This improves flow efficiency and reduces maintenance needs.
PPR Fitting also withstands pressure and thermal cycles reliably.
Its lifespan ranges from 30 to 50 years or more.
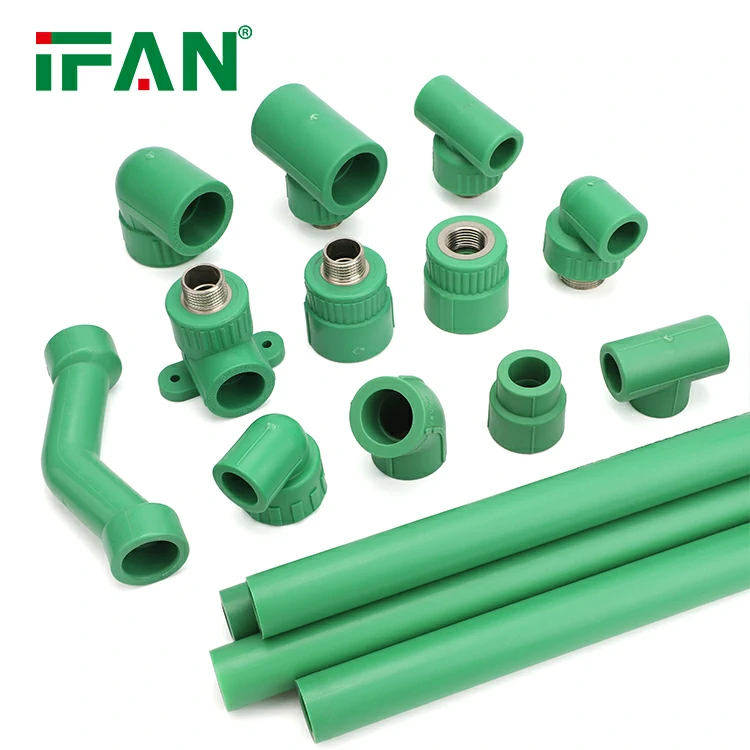
Thermal and Acoustic Performance
PPR Fitting offers excellent thermal insulation properties.
It maintains water temperature with less energy loss.
Copper conducts heat quickly, losing more thermal energy.
For hot water lines, PPR is more energy-efficient.
PPR Fitting also reduces noise from water hammer.
Copper pipes may generate noticeable sounds during pressure changes.
For sound-sensitive environments, plastic pipes are a better choice.
This makes PPR preferred in residential or hotel applications.
Cost Comparison
PPR Fitting is generally less expensive than copper.
Copper prices fluctuate due to global metal markets.
Installation cost for copper is also higher.
It needs specialized labor and more installation time.
PP-R Fitting offers lower material and labor costs overall.
For budget-sensitive projects, this makes a significant difference.
However, long-term costs also depend on system longevity and repairs.
Both options can be cost-effective with proper planning.
Environmental and Safety Aspects
PP-R Fitting is recyclable and chemically inert.
It does not corrode or release harmful substances into water.
Copper is natural but mining and refining impact the environment.
Lead solder use is now restricted for safety reasons.
PPR Fittings use thermal welding, eliminating toxic adhesives or flux.
It’s widely approved for drinking water in many regions.
Both materials are safe when installed according to regulations.
PPR offers slightly more eco-friendly and health-safe advantages.
Final Verdict and Application Guide
PPR Fitting is ideal for residential water systems and heating lines.
It is cost-effective, corrosion-free, and easy to install.
Copper fittings suit high-temperature, high-pressure, or visible installations.
It’s often used in hospitals, commercial kitchens, and fire systems.
In areas with acidic or hard water, PPR Fitting performs better.
For outdoor use, copper may resist UV better than plastic.
Both options are reliable if chosen for the right application.
The best choice depends on your specific project priorities.