High-Density Polyethylene (HDPE) pipes and connectors are known for their durability, but proper installation, maintenance, and environmental considerations are crucial for maximizing their lifespan (typically 50–100 years). Below are key strategies to ensure long-term performance.
1. HDPE Pipe Connectors Proper Installation Techniques
✅ Follow Manufacturer Guidelines
- Use recommended fusion temperatures, pressures, and cooling times.
- Ensure proper alignment to avoid stress concentrations.
✅ Avoid Common Mistakes
- Cold Welds: Incomplete fusion due to insufficient heat or pressure.
- Contamination: Dirt, grease, or moisture during fusion weakens joints.
- Over-Tightening Mechanical Fittings: Can deform HDPE, leading to leaks.
✅ Post-Installation Checks
- Conduct pressure testing (hydrostatic or pneumatic) before use.
- Inspect for visual defects (uneven beads in fusion, gaps in mechanical joints).
2. Material & Environmental Considerations
✅ UV Protection for Above-Ground Pipes
- Use black HDPE (carbon-black stabilized) or apply protective coatings.
- Shield pipes from direct sunlight with insulation or enclosures.
✅ Thermal Expansion & Contraction
- Allow for movement in above-ground installations (use expansion loops).
- Avoid rigid anchoring—use flexible supports where needed.
✅ Chemical & Abrasion Resistance
- Confirm HDPE grade (PE80, PE100) is compatible with transported fluids.
- For abrasive slurries (mining, dredging), consider wear-resistant liners.
✅ Underground Installation Best Practices
- Use proper bedding (sand/gravel) to avoid point loads.
- Ensure trench depth meets local codes (prevents freezing/crushing).
3. Regular Inspection & Maintenance
✅ For Mechanical Fittings:
- Periodically check gaskets and bolts for wear.
- Re-torque if necessary (but avoid over-tightening).
✅ For Fusion Joints:
- Although maintenance-free, inspect for stress cracks near welds.
- Use non-destructive testing (NDT) like ultrasonic testing for critical pipelines.
✅ Leak Detection
- Monitor pressure drops in closed systems.
- For buried pipes, use acoustic sensors or tracer wire systems.
4. Protection Against External Damage
✅ From Construction Activities
- Mark buried HDPE lines with warning tape or tracer wires.
- Use concrete slabs or protective sleeves in high-traffic areas.
✅ From Rodents & Root Intrusion
- Install root barriers near trees.
- Use rodent-resistant conduit where necessary.
5. Handling & Storage Before Installation
✅ Avoid Improper Storage
- Store pipes horizontally on flat surfaces (not stacked too high).
- Keep away from direct sunlight, extreme heat, or chemicals.
✅ Prevent Scratches & Dents
- Use nylon slings (not metal hooks) for lifting.
- Avoid dragging pipes on rough surfaces.
6. System Design for Longevity
✅ Minimize Stress Points
- HDPE Pipe Connectors,Use proper bends (not sharp angles) to reduce fatigue.
- Avoid excessive deflection (follow pipe stiffness ratings).
✅ Corrosion Prevention in Hybrid Systems
- When connecting to metal pipes, use dielectric unions to prevent galvanic corrosion.
Troubleshooting Common Issue
Problem | Possible Cause | Solution |
---|---|---|
Leaks at joints | Poor fusion, misalignment, or gasket failure | Re-weld or replace fitting; inspect gaskets |
Cracking over time | UV degradation, thermal stress, or improper support | Replace with UV-stabilized HDPE; add expansion joints |
Reduced flow | Sediment buildup or pipe collapse | Flush system; check for external loads |
Final Recommendations
✔ For underground systems → Ensure proper bedding and avoid sharp rocks.
✔ For high-pressure applications → Use butt fusion with certified welders.
✔ For corrosive environments → Verify chemical compatibility of HDPE grade.
View more:https://www.ifanfittings.com/
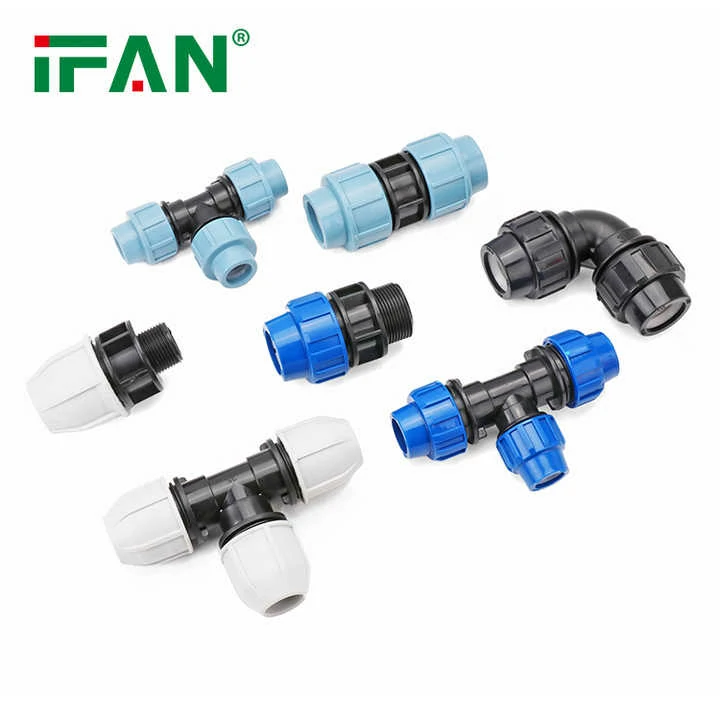