High-density polyethylene (HDPE) piping relies on corresponding fittings to create functional systems. This article explores the fittings made specifically for HDPE pipes and the techniques used to produce strong, sealed connections critical for performance.IFAN factory has 30+ years of manufacturing experience supporting color/size customization support free samples. Welcome to consult for catalog and free samples. This is our Facebook Website: www.facebook.com
1. What are HDPE Pipe Fittings?
HDPE pipe fittings are components used to connect HDPE pipes. They allow changing direction, branching, changing size, shutting off flow, or joining pipes to other system parts.
HDPE fittings mate with the standardized outside diameters of HDPE pipes. They provide either permanent welded joints or removable mechanical joints.
Common types of HDPE fittings include elbows, tees, reducers, stubs, caps, couples, adapters, flanges, and ball valves. Custom fabrication produces large-diameter HDPE headers, manifolds, laterals, and connector spool pieces.
2. Key Properties of HDPE Fittings
HDPE fittings possess the same properties that make HDPE an exceptional piping material:
- High strength and stiffness – Fittings remain rigid under pressure.
- Corrosion and chemical resistance – HDPE withstands water, salts, acids, and many chemicals.
- Thermal endurance – Fittings perform through hot or freezing temperatures.
- Low friction – Smooth water flow through fittings.
- Freeze/thaw resilience – Fittings flex without cracking.
Proper materials selection ensures HDPE fittings provide the same long service life as the piping. Approved HDPE fittings maintain water purity and do not leach contaminants.
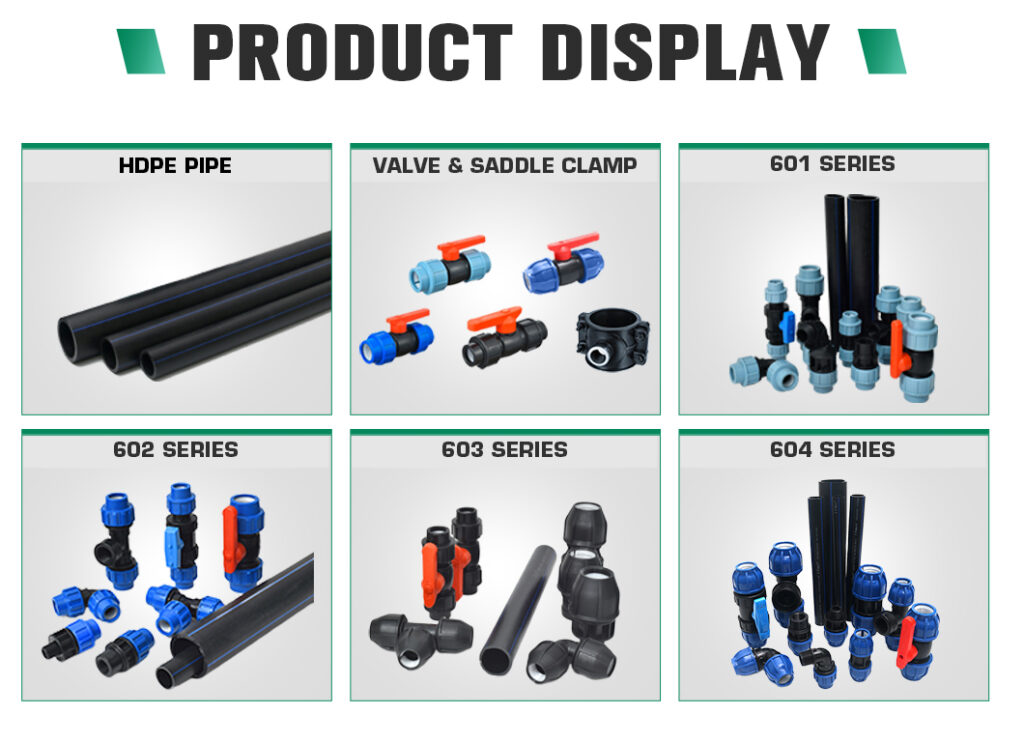
3. Joining Methods for HDPE Pipe Fittings
Several techniques permanently connect HDPE fittings to HDPE pipes:
Butt Fusion – Pipe ends and fitting surfaces get heated and pressed together, fusing into a monolithic joint. Produces the strongest, most leak-proof connection.
Socket Fusion – A heated tool round fuses the inside of a fitting socket to the outside of a pipe end inserted into it.
Electrofusion – Electric current applied to wire coils around the joint area fuses the pipe and fitting. Often used in field installations.
Fabricated Fittings – Large custom fittings get machined from HDPE stock material and welded onto pipe sections.
Mechanical fittings use steel retaining rings to compress gaskets between grooved or flanged HDPE components. Bolts allow the disassembly of joints.
Permanent fusion welding creates leak-free HDPE fitting connections that have performed consistently over decades. Field joint integrity testing validates proper installation.
4. HDPE pipe fittings Cold Expansion Fittings for Plastic Pipe Connections
For minor repairs or additions, cold expansion fittings provide a simple method to tap new branch lines into existing HDPE pipes.
A hole saw or drill penetrates the pressurized main pipe. The outlet branch fitting gets inserted and expanded using a swaging tool. The mechanical sealing pressure between the fitting and the main pipe creates a permanent, leak-free connection.
Cold expansion fittings eliminate the need for fusion equipment. Branch lines can be installed without the system shut down. Saddle and tee fittings accommodate outlets from 1/2″ to 2″ in diameter.
5. HDPE pipe fittings are Transition Fittings Connecting HDPE to Other Materials
Where HDPE piping interfaces with other materials, transition fittings enable connections:
- HDPE x PVC or CPVC – Chemically fused or mechanically coupled plastic pipe joints.
- HDPE x Ductile iron – Flanged connectors withstand pressure differentials.
- HDPE x Carbon steel – Mechanical couplings make convenient field connections.
- HDPE x PEX – Plastic tubing adapters make for easy plumbing additions.
Having a range of transition fitting options prevents limiting HDPE to isolated system sections. Building HDPE into piping networks gets simplified.
6. Fabricated HDPE Fittings For Large Pipe Sizes
For large-diameter sewers, storm drains, and industrial piping using 24” to 60” HDPE pipes, custom-fabricated fittings provide appropriate transitions.
Flanges, elbows, laterals, wyes, and headers of HDPE stock get machined and butt welded onto pipe sections. This fuses fittings to create mammoth piping assemblies transporting high volumes.
Onsite fusion welding capability allows engineers to configure fabricated HDPE fittings in inefficient piping networks. Curved radius elbows promote smooth hydraulic flow.
7. Proper HDPE Fitting Installation Procedures
To achieve optimal performance, HDPE fittings get installed using the following proper techniques:
- Matching fitting and pipe dimensions precisely
- Cutting pipes squarely with sharp cutting tools
- Facing pipe ends and fitting sockets perfectly perpendicular
- Cleaning joining surfaces thoroughly before fusion
- Applying even heat and pressure during electrofusion or socket fusion processes
- Allowing completed joints to cool properly before handling
Following manufacturer specifications for temperatures, pressures, alignment, and dwell times produces strong, sealed fittings. Allowing adequate cooling prevents weak bonds.
For mechanical joints, properly torquing fasteners compresses gaskets evenly without distortion. Avoiding overtightening prevents cracking. Lubricating gaskets ease assembly without contaminating water.
8. Why HDPE Fittings are advantageous
HDPE fittings provide advantages over metal fittings in many applications:
- Easier, faster installation by fusion welding instead of threading or flanging
- Leak-free connections without corrosion over time
- The self-restraint of butt-fused joints eliminates the need for thrust-blocking
- Ability to divert flow with minimal head loss due to smooth interior walls
- Withstands freezing, thawing, and soil movement without leaks
- Fabrication of custom fittings for large-diameter piping
- Lightweight compared to concrete, iron, or steel fittings
- Easy to extend existing HDPE piping by electrofusion
HDPE fittings serve critical functions in assembling piping networks spanning from homes to public utility systems. Correct selection and joining enable taking full advantage of HDPE piping’s beneficial properties.
9. HDPE Outlets and Connection Fittings
HDPE outlet fittings allow tying into main or branch piping lines. Connection fittings join HDPE pipe to system equipment.
Common outlet and connection HDPE fittings include:
- Tees – Branch off from main pipes to feed secondary lines.
- Wyes – Make 45 or 90-degree side outlets from the main run.
- Laterals – Tap directly off larger mains or headers.
- Elbow Outlets – Provide directional branch lines.
- Crosses – Intersect multiple branch lines.
- Adapters – Connect HDPE pipes to valves, pumps, and appliances.
- Flange Adapters – Join HDPE to flanged components like backflow preventers.
Whether fusion welded or mechanically coupled, properly installed HDPE outlets and connection fittings withstand the rigors of continuous system operation. Their integrity supports overall piping network functionality.
10. The Future of HDPE Fittings
As HDPE pipes gain increased acceptance for plumbing systems, manufacturers continue expanding fitting options. Newly developed fittings aim to simplify connections and widen HDPE piping applications.
Some innovations include:
- Large diameter fabricated wyes replacing clumsy multi-piece assemblies
- Electrofusion-reducing couplings for transitioning pipe sizes
- Quick connect fittings for industrial and appliance interfaces
- Diffuser adapters to reduce outlet velocities from large pipes
With expanded fitting capabilities, engineers obtain greater design freedom to exploit HDPE’s advantages. Improved connection methods also enable faster and lower-cost installations.
11. HDPE Fittings Enable System Functionality
From major municipal piping backbone to final building outlets, the properly chosen HDPE fittings make assembled polyethylene piping systems possible. Correct fusion joining preserves HDPE’s virtues of leak-free performance and long service lifetimes.
By bridging pipes, controlling flows, and allowing pipe connections, HDPE fittings serve the vital role of fulfilling system configurations for transporting critical fluids safely, efficiently, and reliably over decades.