PPR (Polypropylene Random Copolymer) pipe welding machines are designed to create strong, reliable, and leak-proof joints through a process called fusion welding or butt fusion welding. This process involves heating the ends of the pipe and fitting to a precise temperature and then applying controlled pressure to fuse them together, resulting in a homogeneous and durable joint. Below are the key ways in which PPR pipe welding machines ensure the creation of strong and durable joints:
1. Precise Temperature Control
- How It Works: PPR pipe welding machines use digital or analog temperature control systems to regulate the heating plate’s temperature. The machine ensures that the heating plate reaches and maintains the optimal temperature for the specific type of PPR material, usually between 200°C and 260°C.
- Why It’s Important: Maintaining the correct welding temperature is crucial for melting the surfaces of the pipe and fitting without damaging the material. Precise temperature control ensures that the molten material from both the pipe and fitting fuse seamlessly, creating a solid bond.
2. Uniform Heating and Fusion
- How It Works: The heating plate or fusion plate in a PPR pipe welding machine applies heat evenly across the surfaces of the pipe and fitting. Some machines use specialized heating elements or non-stick coatings to ensure uniform heat distribution.
- Why It’s Important: For a joint to be strong and durable, both the pipe and the fitting need to be heated evenly to the correct temperature. If one side of the joint is hotter than the other, the materials will not fuse properly, which can lead to weak spots, leaks, or premature failure. Uniform heating guarantees that the molten surfaces fuse together uniformly, resulting in a robust and consistent joint.
3. Controlled Pressure Application
- How It Works: The pressure is adjustable based on pipe size and welding specifications.
- Why It’s Important: Proper pressure is essential for achieving a strong joint. If too little pressure is applied, the two pieces may not fuse completely, leaving air pockets or weak connections. If excessive pressure is applied, the material may be forced out, compromising the integrity of the joint.
4. Proper Alignment of Pipe and Fitting
- How It Works: PPR pipe welding machines are equipped with clamps or holders that precisely align the pipe and fitting during the welding process. These fixtures prevent any movement during heating, fusion, and cooling stages.
- Why It’s Important: Misalignment can lead to poorly fused joints that are weak or uneven. Proper alignment ensures that the pipe and fitting are perfectly matched during the welding process, allowing the surfaces to melt evenly and form a uniform joint. This alignment reduces the risk of weak spots, misfused areas, or leakage points, which could compromise the integrity of the entire piping system.
5. Controlled Cooling Time
- How It Works: After the pipe and fitting are fused together, the welding machine allows the joint to cool down under controlled conditions. Many machines incorporate cooling fans or cooling plates to regulate the cooling process.
- Why It’s Important: The cooling process is just as critical as heating for ensuring a strong joint. If the joint cools too quickly, it may lead to internal stresses, cracks, or deformation. Controlled cooling allows the molten material to solidify evenly, ensuring the joint is stable and structurally sound. Proper cooling also helps to prevent distortion or damage to the pipe.
6. Use of High-Quality Fusion Plates
- How It Works: The fusion plate (heating plate) used in PPR pipe welding machines is typically made from high-quality aluminum or steel with a non-stick surface. The plate must be durable and capable of maintaining a consistent temperature.
- Why It’s Important: The fusion plate plays a crucial role in ensuring even heat distribution and preventing overheating or damage to the pipe and fitting. Additionally, a non-stick surface prevents material residue buildup, maintaining the plate’s efficiency and consistency over time.
8. Consistent Pressure During Fusion
- How It Works: Once the pipe and fitting are heated, the welding machine applies a steady, even amount of pressure to force the two pieces together. The pressure is maintained for a specified duration, allowing the surfaces to fuse completely.
- Why It’s Important: Constant pressure is necessary to ensure that the molten surfaces of the pipe and fitting bond together uniformly. If the pressure fluctuates, it could result in incomplete fusion or an uneven joint. Consistent pressure creates a solid connection, which is key to the strength and durability of the joint.
9. High-Quality Materials
- How It Works: PPR pipe welding machines are designed to work with high-quality PPR pipes and fittings. The strength and durability of the joint also depend on the quality of the materials used in the welding process.
- Why It’s Important: High-quality PPR materials are more resistant to cracking, thermal expansion, and degradation over time, leading to more durable joints.
Conclusion: Creating Strong and Durable Joints
PPR pipe welding machines ensure strong, durable joints by maintaining precise temperature control, applying consistent pressure, ensuring uniform heating, and maintaining proper alignment throughout the process.
View more:https://www.ifanfittings.com/
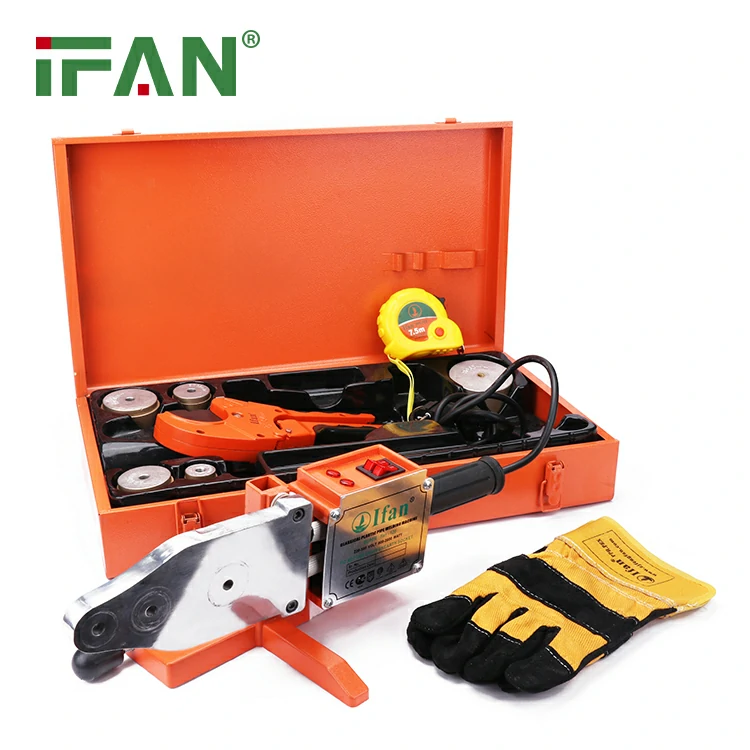