As the world’s population continues to grow, the importance of efficient and effective irrigation strategies has become increasingly apparent. HDPE (high-density polyethylene) irrigation fittings have proven to be a reliable and cost-effective solution for many agricultural applications. In this blog post, we will explore the production processes used to create these vital components.
Extrusion
The primary method for producing HDPE irrigation fittings is through extrusion. Extrusion is a manufacturing process whereby material is forced through a die to create a specific shape or profile. The process begins with raw HDPE pellets, which are fed into an extruder barrel. Within the extruder barrel, heat and pressure are applied to melt and soften the material. Once the material is sufficiently softened, it is forced through a die that has the desired shape of the fitting. The extruded fittings are then cut to the desired length and cooled.
Injection Molding
Injection molding is another method used to produce HDPE irrigation fittings. Injection molding involves injecting molten HDPE material into a mold cavity under high pressure. The molten material is then allowed to cool and solidify, taking on the shape of the mold. Injection molding allows for the production of more complex parts and higher production rates than extrusion.
Fusion Welding
One of the unique characteristics of HDPE is its ability to be fusion welded. Fusion welding involves using heat to melt and fuse two HDPE fittings together, creating a seamless connection. Fusion welding is a critical stage in the production of it, as it ensures that connections are leak-free and structurally sound.
Finishing
After extrusion or injection molding, HDPE irrigation fittings are often finished with additional processes to improve the function and appearance of the final product. Examples of finishing processes include drilling holes for attachment, machining surfaces for improved fit and sealing, and adding labels or branding.
Quality Control
Throughout the production process, quality control measures are implemented to ensure that HDPE irrigation fittings meet the required specifications and standards. These measures include testing raw materials for quality and consistency, conducting in-process inspections to identify defects or inconsistencies, and performing final product testing to ensure that fittings meet performance requirements, such as pressure and flow rate.
In conclusion
The production processes for HDPE irrigation fittings involve a combination of extrusion, injection molding, fusion welding, and finishing. Each step is critical to producing reliable and cost-effective fittings for agricultural irrigation systems. With increasing demand for efficient and sustainable irrigation strategies, the importance of high-quality HDPE irrigation fittings continues to grow.
View more:https://www.ifanfittings.com/
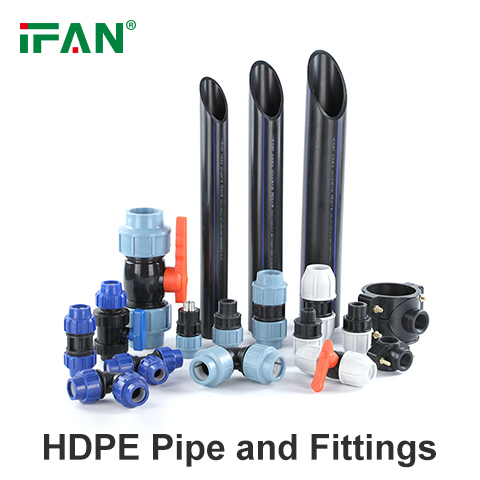