High-density polyethylene (HDPE) has emerged as a highly useful piping material for potable water service, sewer systems, and other plumbing applications. This article explores the science and engineering behind HDPE pipes that make them advantageous piping solutions.
What is an HDPE Pipe?
HDPE pipe is a rigid plastic pipe made from polyethylene thermoplastic. The material gets produced into a pipe through a process called extrusion. HDPE resin gets heated and formed into a hollow tube shape as it passes through a shaping die.
The “high density” in HDPE describes the molecular structure of the polyethylene. HDPE molecules have less branching and bond tighter than low-density polyethylene. This gives HDPE superior physical and chemical properties.IFAN factory has 30+ years of manufacturing experience supporting color/size customization support free samples.Welcome to consult for catalog and free samples. This is our Facebook Website: www.facebook.com
Properties of HDPE Pipe
HDPE pipe offers properties that make it highly useful for plumbing systems:
- High tensile strength – HDPE pipe withstands high pressures without damage.
- Hardness and rigidity – Pipes maintain their shape without deformation.
- Low friction coefficient – Smooth interior minimizes flow resistance.
- Corrosion resistance – HDPE pipes are inert to water chemistry and salt.
- Freeze resistance – The material remains flexible to -60°F without cracking.
- Thermal insulation – Low conductivity keeps fluid temperatures stable.
- Lightweight – HDPE pipes are easier to handle and require less support.
The combination of strength, chemical resistance, and temperature endurance make HDPE ideal for transporting potable water, sewage, slurries, chemicals, and compressed gasses.
Joining Methods for HDPE Pipe
Several techniques effectively join HDPE pipe into sealed systems:
Butt Fusion – Pipe ends get melted and fused together, forming monolithic joints stronger than the original pipe. Requires special fusion machines to align and heat-weld pipes.
Socket Fusion – A heating tool fuses the inside of a shaped HDPE socket end to a pipe end inserted into it. Produces smooth permanent joints.
Electrofusion – Electric coils pre-fitted inside HDPE fittings generate heat to melt the joint. Often used for field repairs and additions.
Mechanical Connections – Stainless steel clamps compress gaskets between grooved or flanged HDPE pipes to seal joints. Allows disassembly.
Transition fittings join HDPE to other piping materials like PVC, ductile iron, and steel. HDPE’s weldability allows reliable, permanent leak-proof piping networks.
HDPE Pipe Sizes and Dimension Ratios
HDPE pipes cover a range of diameters from 1⁄2” to 65”. Smaller diameters suit tight plumbing spaces while large sizes handle heavy flows in sewers, storm drains, and industrial uses.
HDPE pipe dimensions follow standardized sizing conventions such as CTS (copper tube size) and IPS (iron pipe size). This enables connecting HDPE to common fittings and appurtenances.
Dimension Ratio (DR) indicates the ratio of pipe diameter to wall thickness. Lower DR indicates thicker walls, with higher pressure ratings and stiffness. DR 7 to DR 17 HDPE pipes suit most pressure plumbing applications.
Pipe section lengths are commonly available up to 50 feet. Long sections reduce the number of joints needed compared to shorter metal or PVC pipe lengths. Fewer joints enhance system integrity.
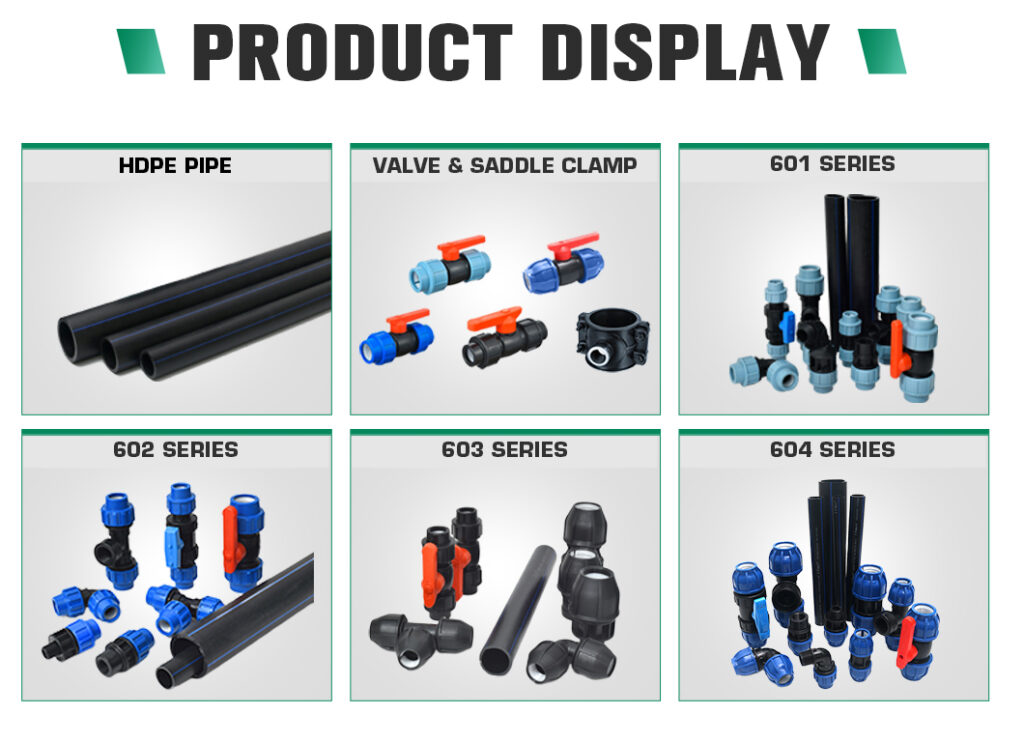
HDPE Pipe Pressure Ratings
The PPI (Plastic Pipe Institute) has standardized long-term pressure ratings for HDPE pipe based on testing. For water at 73°F, pressure ratings for DR 9 HDPE pipe are:
- 160 PSI for 1⁄2” – 1 1⁄4” diameters
- 125 PSI for 1 1⁄2” – 3” diameters
- 100 PSI for 4” – 65” diameters
Thicker DR 7 and DR 11 pipes offer higher pressure capacities. Pipe pressure ratings account for typical peak flows and safety factors.
Actual design pressures for buried HDPE piping consider soil constraints, surge pressures, and installation handling. Long-term performance relies on proper fusion joining without defects.
HDPE for Potable Water Systems
HDPE pipes approved by NSF International meet standards for potable water service. The inert HDPE material does not leach chemicals or harbor bacteria. Water flows smoothly through slick HDPE pipes with minimal disinfectant loss.
Municipal water systems take advantage of HDPE pipes in buried distribution mains. The material resists corrosion and tuberculation that commonly plague metal pipes. Lightweight HDPE also reduces transport and handling costs.
Within buildings, HDPE distributes pressurized water to fixtures and appliances. No special isolation from other building materials is needed. Proper support allows HDPE to handle high-rise vertical plumbing.
For potable services, only high-purity HDPE resins are used. Careful butt fusion joining preserves drinking water integrity. HDPE lasts decades in municipal and residential water systems.
HDPE Pipe in Drain-Waste-Vent Systems
HDPE also gets utilized for buried building drainage systems. The chemical resistance handles corrosive effluents in large-diameter drains. In toxic chemical plants, HDPE containment piping safely directs hazardous waste.
Below-grade non-pressure drainage applications take advantage of HDPE’s flexibility. Pipes can snake around obstructions without needing many fitted joints. The smooth bore maintains flow without buildup.
Special foam-core HDPE pipes provide insulation that prevents condensation on cold drain water. Vent stacks through roofs benefit from HDPE’s lightweight compared to cast iron. HDPE stands up to effluent gases and temperature fluctuations.
Central sewer collection systems gain economies from long HDPE mains. The fusion weldability allows engineers to specify HDPE for customized large-diameter piping layouts spanning miles. Trenchless directional drilling enables the installation of HDPE sewer pipes without extensive excavation.
HDPE for Geothermal and District Energy Piping
HDPE performs well in geo-exchange systems that take advantage of shallow earth temperatures. The flexibility accommodates shifts and settling. Direct burial reduces installation costs.
With fusion welding, engineers can configure U-shaped ground loops or Slinky-like heat exchanger arrays from long HDPE pipe lengths. Large-scale geothermal fields also utilize HDPE supply and return piping for decades of service.
District energy systems take advantage of HDPE pipes for underground steam, heating water, and chilled water transport between central plants and buildings. The insulation and temperature resistance minimize energy losses across networks.
NUPipes in Narrow Tunnels
In crowded underground utility corridors, smaller diameter “NUPipe” provides efficient heat and energy distribution. The flexible HDPE material accommodates tight installation bends. Though narrow, NUPipe handles substantial flows thanks to slick interior walls.
Performance in Cold Climate Installations
HDPE retains ductile flexibility and impact resistance in sub-freezing ground temperatures. Pipes withstand seasonal freeze/thaw cycles without cracking. Sound fusion joints prevent deterioration.
Building plumbing in cold regions benefits from HDPE’s ability to endure expansion and contraction stresses. Pipes maintain free-draining slopes without sagging. For pipes above ground, insulation limits heat loss and condensation.
Suspended or Exposed HDPE Piping
Though designed for burial, HDPE pipes often get installed in suspended or exposed runs. Hanger spacing follows engineering guidelines to prevent excessive deflection under pressure and weight loads.
In tanks, channels, and containment sumps, HDPE piping withstands exposure to UV light and extreme temperature fluctuations. The inert material resists damage from spills or immersion in many chemicals.
Proper fusion techniques ensure suspended HDPE pipelines achieve the 150-year design life. Anchoring allows the piping to accommodate thermal expansion and building shifts. Carefully engineered supports prevent over-stressing pipe joints.
HDPE Pipe Field Handling and Installation
Transporting and installing HDPE pipes requires attention to protecting the integrity of the material. Stringent procedures safeguard pipes from risks such as:
- Gouging or abrasion during loading/unloading
- Crushing or flattening from improper storage
- Warping or distorting when near heat sources
- Surface contamination exposure
- Excessive bending strain during layout
Crews take care not to drag or roll pipes over sharp objects. Padding cushions points of contact. Pipes get fused shortly after delivery while surfaces remain clean.
Trench bottom preparation removes sharp rocks. Bedding cushions provide firm uniform support once buried. Backfill gets screened and compacted in layers to stabilize pipes.
HDPE Advantages over Steel, PVC, and Concrete Pipes
Compared to traditional piping materials, HDPE offers important advantages:
- Corrosion resistance exceeds even stainless steel
- Lower installation costs than heavy concrete or steel
- No leakage risk from failed pipe joints or seals
- Better flow rates than small-diameter PVC
- Ability to field repair leaks by re-fusing
- Less accumulation of mineral deposits than metal
- Long lifetimes with greater reliability
The combination of toughness, chemical resistance, lightweight, and leak-free fusion joints provides HDPE piping performance unachievable with legacy materials.
HDPE Pipe Lifespan and Testing
Properly handled and installed HDPE pipe is engineered to last over 100 years underground. Fitness-for-service testing per ASTM F2881 provides field assurance of fusion joint soundness and system integrity.
For critical systems, non-destructive electromagnetic testing identifies potential pipe defects during manufacturing and construction. Periodic inspection verifies pipelines remain in serviceable condition.
HDPE pipes endure for decades across a wide range of community plumbing applications. The material science behind high-density polyethylene makes it a highly 20th-century plumbing product with many advantages over old piping technologies.