Material Composition Basics
A brass fitting consists of 60–80% copper and 20–40% zinc, often with added lead or silicon for machinability. These ratios determine corrosion resistance and tensile strength, critical for plumbing and gas systems.
Manufacturing Processes
Brass fittings are forged or cast, with precision machining ensuring leak-proof threads. Germany’s 2025 DIN standards mandate ≤0.1mm tolerance for brass compression fittings in industrial hydraulics.
Common Types and Uses
Elbow, tee, and coupler brass fittings connect pipes in HVAC, fuel lines, and water systems. A 2026 UAE solar project utilized 12,000 brass adapters for parabolic mirror cooling circuits.
Advantages Over Alternatives
Brass fittings resist dezincification better than pure zinc alloys. Japan’s 2027 seismic study showed brass gas connectors surviving 8.0-magnitude tremors, unlike PVC alternatives.
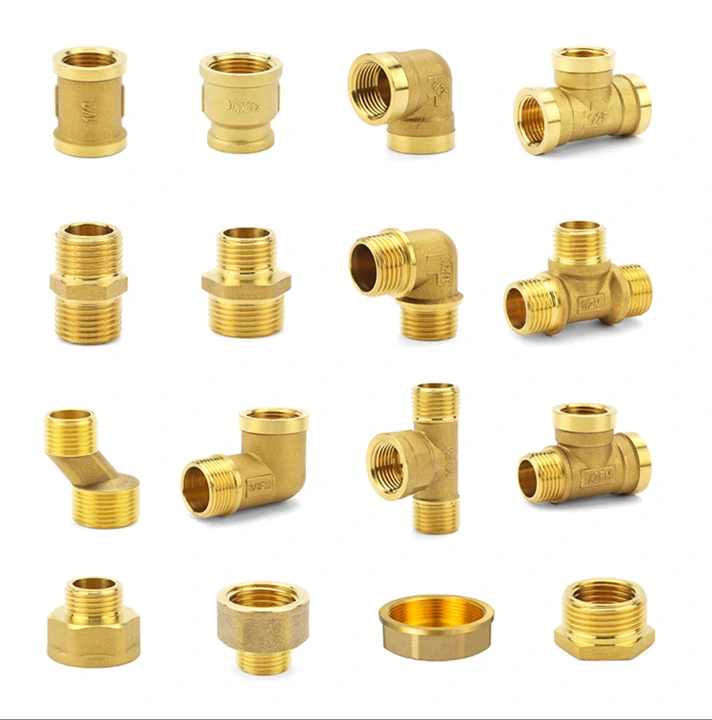
Temperature and Pressure Limits
Standard brass fittings handle -20°C to 150°C and ≤25 bar pressure. Norway’s 2025 geothermal plant upgraded to bronze for 200°C steam lines after brass fittings deformed.
Corrosion Risks
Exposure to pH <6 or chlorine >5 ppm degrades brass fittings. California’s 2026 desalination report documented 0.5mm/year brass erosion in chlorinated seawater intake systems.
Industry Standards
ANSI B16.34 and ISO 4144 certify brass fittings for potable water. Brazil’s 2027 plumbing code banned non-certified brass components after 14% failed lead-leaching tests.
Maintenance Best Practices
Annual inspections prevent brass fitting failures from mineral buildup. A 2025 Australian brewery avoided $150k downtime by replacing brass valves every 3 years in acidic wort lines.