Introduction
High-density polyethylene (HDPE) pipe is widely used in various applications, including water distribution, sewage systems, and irrigation. Attaching HDPE pipe requires specific techniques and tools to ensure a secure and reliable connection. This article will guide you through the process of attaching HDPE pipe.
Preparation and Tools
Before attaching HDPE pipe, ensure you have the necessary tools and materials. This includes a pipe cutter, HDPE pipe and fittings, primer, and either a butt fusion welder or a socket fusion welder, depending on the fitting type. HDPE primer helps create a bond between the pipe and fitting.
Cutting the Pipe
Use a pipe cutter designed for HDPE to cut the pipe to the desired length. Measure accurately to avoid waste and ensure a proper fit. Mark the cut line with a pencil and cut slowly to avoid jagged edges.
Preparing the Pipe and Fitting
Once the pipe is cut, clean the end of the pipe and the inside of the fitting thoroughly. Remove any debris, dirt, or moisture. Apply HDPE primer to both surfaces to prepare them for welding. Allow the primer to dry completely before proceeding.
Choosing the Fusion Method
There are two common fusion methods for attaching HDPE pipe: butt fusion and socket fusion. Butt fusion is used for joining straight lengths of pipe, while socket fusion is used for connecting pipes to fittings. Choose the appropriate method based on your application and the type of fitting you are using.
Performing the Fusion Weld
For butt fusion, align the ends of the two pipes and insert them into the butt fusion machine. The machine will heat the ends of the pipes until they melt, then press them together to form a seamless connection. For socket fusion, insert the end of the pipe into the socket of the fitting and use the socket fusion machine to heat and fuse the connection.
Cooling and Inspection
After welding, allow the connection to cool completely. This is crucial for the HDPE material to set and form a strong bond. Once cooled, visually inspect the connection for any imperfections or flaws. If everything looks good, you can proceed with testing the system.
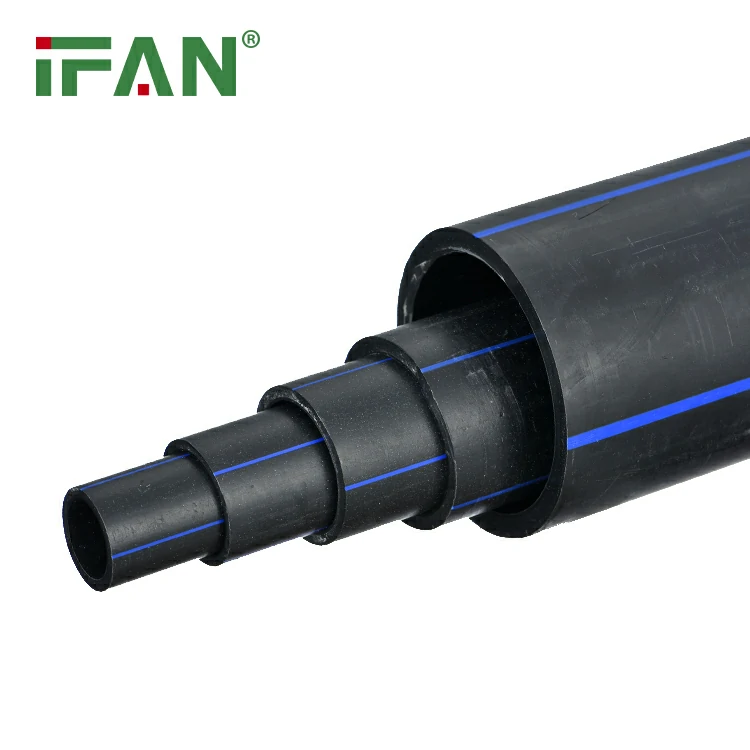
Testing the Connection
Before putting the system into use, test the connection for leaks. Apply pressure to the system and monitor the connection for any signs of leakage. Use soapy water or a leak detection spray to help identify any leaks. If leaks are found, repair them immediately and retest.
Example of Attaching HDPE Pipe
For example, let’s say you are installing an HDPE water distribution system in a residential area. You would cut the HDPE pipe to the required length, clean and prime the ends, and then use a butt fusion welder to connect the straight lengths of pipe. For connecting the pipe to a valve fitting, you would use a socket fusion welder to create a secure and reliable connection.
Conclusion
Attaching HDPE pipe requires careful preparation, the right tools, and precise technique. By following these steps, you can ensure a strong and reliable connection that will withstand the pressures and temperatures of the piping system. Always refer to the manufacturer’s instructions and local building codes to ensure compliance and safety. With the right knowledge and tools, attaching HDPE pipe is a straightforward and effective process.